Screen Printing on Polyester
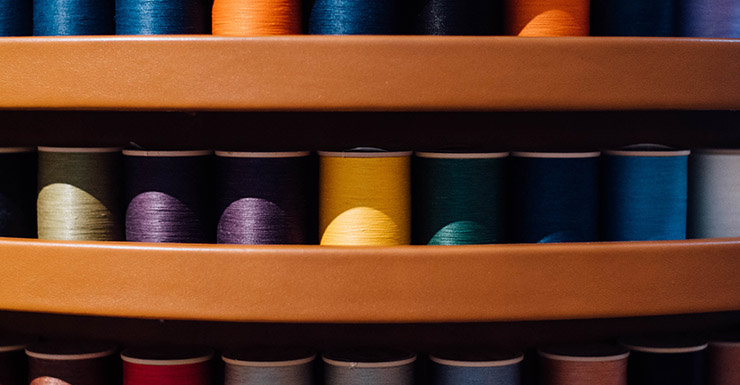
Polyester is one of the fabrics most prone to dye migration, so it is important to make sure to have the best inks at hand for screen printing on polyester t-shirts. Most major screen printing ink manufacturers have ink product lines specifically engineered for polyester fabrics. These special low bleed plastisols are meant to combat dye migration, which is the biggest challenge of screen printing on polyester.
Dye migration is most common and visible with white inks on darker shirt colors such as navy, maroon, red, and certain shades of green. It can materialize immediately or even two weeks later. The most common cause is overheating during the curing process. The dyes in polyester fabric may turn gaseous when heated to 330 degrees Fahrenheit. The other major common cause of dye migration happens through a similar chemical reaction and depends mostly on the quality of the dye in the polyester.
The latter issue can only be prevented by making sure to print on quality polyester t-shirts. The former issue can be prevented through the use of poly specific inks, or through the use of nylon bonding catalyst additives. It is important to make sure to cure all polyester fabrics under 320 degrees Fahrenheit, where it is well below the risks of reaching 330 Fahrenheit. Poly inks are designed to cure at a lower temperature, thus reducing the risk of dye migration as a result of the overheating of the fabric. Nylon bonding catalyst additives also reduce the curing temperature of plastisol inks to further prevent dye migration and can be added to regular plastisol inks. Adding a small amount of the nylon bonding additive also helps to bond the plastisol ink to the fabric.
If you prefer to continue using your regular plastisol inks, colored inks are fine without nylon bonding additives. However, using a low bleed white is a must, either with an additive or the special poly ink. Water based inks generally do not print well on polyester. The nylon bonding catalyst additive works well for 50/50 blends, but polyester special inks are generally the best for 100% polyester.
For best results when screen printing on nylon woven fabrics, such as on a nylon sports jacket or nylon cinch sack, just mix a nylon bonding catalyst additive in your plastisol ink. These nylon bonding agents reduce ink viscosity for a much better print that will prevent it from easily rubbing off, peeling, or cracking. For screen printing with a standard opacity nylon bonding catalyst additive, it is best to use a ratio of one part additive to five parts plastisol ink. In using a high-opacity nylon bonding catalyst additive, it is best to use one part additive to four parts plastisol.
When screen printing on spandex, use a spandesol additive with your plastisol ink. These spandesols can be used on lycra spandex, also known as nylon lycra, to produce a design with an excellent softness and stretch. For the environmentally friendly printer, some major screen printing ink manufacturers now carry a special non-phthalate spandesol ink.
Polyester can be a tough fabric to work with since the curing process needs to be very precise, but polyester is a great fabric for t-shirts, jackets, bags, and other products that can be purchased wholesale. Once you have the science of it worked out, the sky’s the limit.